|
Newsletter February 2022 | Menu of Newsletters
In its continuing efforts to revolutionize
discovery-based research into complex biological systems, Pacific Biosciences
has released its next generation of automated, long-read genomic sequencer with
single molecule, real-time (SMRT) sequencing technology the Sequel
System.
In its continuing efforts to revolutionize
discovery-based research into complex biological systems, Pacific Biosciences
has released its next generation of automated, long-read genomic sequencer with
single molecule, real-time (SMRT) sequencing technology the Sequel
System.
The Sequel System is very multifaceted in operation, says Kevin
Lin, mechanical engineer at Pacific Biosciences. It encompasses robotics,
chemical and biological processing, and photonics. Because its intended to be
used in diverse settings within research and laboratory environments, excessive
ambient vibrations could negatively influence the data sets. So, we needed to
implement a vibration isolation component that not only isolated the sensitive
components from vibrations, but also was sufficiently small, compact, and
integrative.
Internal and external factors can create vibration issues
from buildings housing the system including heating and ventilation systems,
fans, pumps, elevators, adjacent road traffic, nearby construction, loud noise
from aircraft, and weather conditions. These influences cause vibrations as low
as 2Hz that can create strong disturbances in sensitive equipment.
With
our earlier sequencer model, we used air tables for vibration isolation, which,
for the most part, performed adequately, Lin says. But use of the Sequel System
in more diverse locations, where low-frequency vibrations may be present to a
greater or lesser degree, necessitated a vibration isolator that was compact
enough to fit into our much smaller Sequel System and could effectively cancel
out these low-frequency vibrations.
Negative-stiffness vibration
isolation Pacific Biosciences ultimately decided on negative-stiffness
isolation to address their needs. Developed by Minus K Technology,
negative-stiffness isolators use completely passive mechanical technology for
low-frequency vibration isolation without using motors, pumps, or chambers,
making them zero maintenance. Because of their very high vibration isolation
efficiencies, particularly in the low frequencies, negative-stiffness vibration
isolation systems enable vibration- sensitive instruments, such as the Sequel
System, to operate in severe low-vibration environments that wouldnt be
practical with top-performance air tables and other vibration-mitigation
technologies...
Full article... |
Featured Product: BM-6 Bench Top Vibration Isolation
Platform
- Vertical and
horizontal frequencies are weight dependent.
- The vertical
frequency of 2.5 Hz and horizontal frequency of 1.5 Hz are achieved at the
upper limit of the payload range.
- At the lower
limits of the payload range, the vertical frequency is approximately 3.4 Hz and
the horizontal frequency is approximately 2.5 Hz.
The
bench top platform offers better performance than a full size air table in a
package only 4.6 inches tall, and without air!
This vibration isolation
platform reaches a new price point and is extremely easy to use. It offers a
1.5 Hz horizontal natural frequency and a 2.5 Hz vertical natural frequency.
There is only one adjustment. There is no need for air or
electricity.
This is the thinnest, most portable, and most user-friendly
isolator ever offered at this level of performance per dollar.perfect for new
generations of small SPM's that require the highest performance in a very
compact system.
Pricing & Specifications |
MInus K's Assist
with the Building of the JWST Telescope
|
All of the JWST systems-level cryogenic
vacuum tests were performed at the NASA Johnson Space Centers (JSC)
Chamber-A. It is now the largest high-vacuum, cryogenic-optical test chamber
in the world, and made famous for testing the space capsules for NASA's
Apollo mission, with and without the mission crew. It is 55 feet (16.8 meters)
in diameter by 90 feet (27.4 meters) tall. The door weighs 40 tons and is
opened and closed hydraulically. The air in the chamber weighs 25 tons, when
all the air is removed the mass left inside will be the equivalent of half of a
staple.
Diagram of the Cyrogenic Chamber in
which the JWST was tested for space.
For three years, NASA JSC engineers built
and remodeled the chambers interior for the temperature needed to test the
James Webb Space Telescope. Chamber A was retrofitted with the helium shroud,
inboard of the existing liquid-nitrogen shroud and is capable of dropping the
chambers temperature farther down than ever, which is 11 degrees above absolute
zero (11 Kelvin, -439.9 Fahrenheit or -262.1 Celsius).
A key addition
to Chamber A was the addition of a set of six custom Minus K
negative-stiffness vibration isolators. The Minus K passive isolators do
not require air and offer better isolation than air and active isolation
systems. A major factor in the selection of the of the vibration isolators was
that they not only isolate vibration vertically, but also horizontally at less
than 1 Hz.
JWST was designed to work in space where the disturbances
are highly controlled and only come from the spacecraft, while on Earth with
all the ground-based disturbances, such as the pumps and motors, and even
traffic driving by can affect the testing. The Minus K vibration isolators
provided dynamic isolation from external vibration sources to create a near
flight-like disturbance environment.
The isolators utilize Minus K's
patented Thermal Responsive Element (TRE) compensator device, a passive
mechanical device, requiring no air or electricity just like the isolators. The
TRE compensator adjusted the isolators as the temperature changes throughout
the testing at JSC, keeping the JWST in the proper position.
The
Critical Design Review for Spacecraft-to-Optical Telescope Element vibration
isolation system was completed one month earlier than scheduled at the end of
2011. The six Minus K negative-stiffness vibration isolators were installed on
top of Johnson Space Centers Thermal Vacuum Chamber A in March
2014.
JWST needed a support structure inside the vacuum chamber to hold
equipment for the testing. Engineers installed a massive steel platform
suspended from the six vibration isolators via steel rods about 60 feet long
(18.2 meters) each and about 1.5 inches (or 38.1 mm) in diameter, to hold the
telescope and key pieces of test equipment. The sophisticated optical telescope
test equipment included an interferometer, auto-collimating flat mirrors, and a
system of photogrammetry precision surveying cameras in precise relative
alignment inside the chamber while isolated from any sources of vibration, such
as the flow of nitrogen and helium inside the shroud plumbing and the rhythmic
pulsing of vacuum pumps.
Minus K's Involvement
continued...
-How much farther can JWST see than the
Hubble? -Why was it launched from near the
equator? -How cold does the JWST get in
space? -How did origami play into the
trip? -Why 24-karat gold on the
mirrors?
Full article... |
Our 29th Anniversary is on 2/1/22 See the
Milestones & Timeline 1993-2022
 |
Founded in 1993 |
 |
|
Minus K Technology Opens
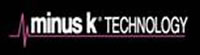
|
|
Minus K Technology opens for business
in February 1993 |
Minus K's original SM-1 patented
Negative-Stiffness passive vibration isolator. This was the first commercialy
available vibration isolator offering 0.5 Hz natural frequencies for both
vertically and horizontally. This was accomplished without the use of air
compressors, computer componets or electricity.
The isolator could be used alone, or in
conjunction with other units, and could be engineered directly into a
system. |
|
Original SM-1 Vibration
Isolator
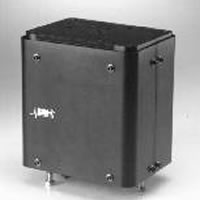 |
Our 29th Anniversary is on 2/1/22 See the
Milestones & Timeline 1993-2022
Within Saint Louis Universitys (SLU)
Department of Physics, research has been ongoing in the development of novel
techniques for synthesis, characterization and measurement of low dimensional
(1D and 2D) systems. This is in hopes to better understand how size, geometry
or interfacing various materials and nanostructures influences the properties
of the resulting systems.
Nanolithography Research
Nanolithography in general terms is concerned with the study and
application of fabricating nanometer-scale structures, meaning patterns with at
least one lateral dimension between 1 and 100 nm. A prime focus is very
largescale integration (VLSI) and ultralarge-scale integration (ULSI)
technology of nanoelectromechanical (NEMS) systems, and the need for better
atomic-scale understanding of issues arising from the miniaturization of
silicon devices. Under the direction of Dr. Irma Kuljanishvili, who heads up
SLUs nanomaterials and nanofabrication research lab, the groups focus is on
This approach is similar to a technique known as dip pen
nanolithography.
In this technique, AFM tips or sharp needles can be
employed to transfer small, femtoliter volumes of molecular solutions, or other
liquid-based ink, to predefined locations on the surface of
samples.
Carbon nanotubes, grapheme and other atomically monolayered
materials are being considered as prime candidates for nanoscale science and
technology applications, due to their unique and superior combination of
electrical, thermal, optical and mechanical properties, says
Kuljanishvili.
SLU's Negative-Stiffness Vibration
Isolation System
Full article... |
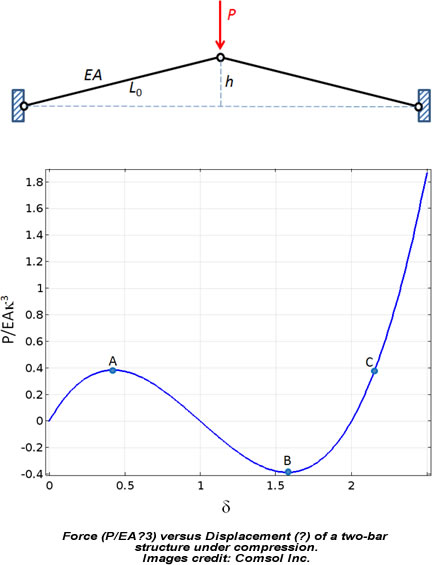
Notice that between points A and B,
displacement is increasing while force is decreasing. Thus, the
structures stiffness is negative in that region.
Negative-stiffness vibration isolators
consist of a horizontal isolator and a vertical isolator connected in series.
To counter motions that involve rotation (pitch and roll), a tilt motion pad
can also be connected in series with the horizontal and vertical isolators.
The horizontal isolator consists of two fixed-free vertical beams
(columns) supporting a weight. The weight imparts both eccentric (off-axis)
axial compressive load and a transverse bending load. This phenomenon is
referred to as the beam-column effect and causes the lateral bending stiffness
of the beams to decrease. In effect, the isolator is acting as a horizontal
spring with a negative-stiffness mechanism.
The horizontal isolator is designed to
take advantage of the beam-column effect, allowing it to act like a
negative-stiffness mechanism.
Vertical motion is addressed using two
horizontal flexures loaded in compression, which form a negative-stiffness
mechanism. The flexures are supported at their outer ends and connected to a
stiff spring at their inner ends. The stiffness of the isolator is determined
by the design of the flexures and by their compressive load.
Two flexures, fixed at their outer ends
and connected to a spring at their inner ends, form a negative-stiffness
mechanism that isolates equipment from vertical motion due to
vibrations.
Full article... |
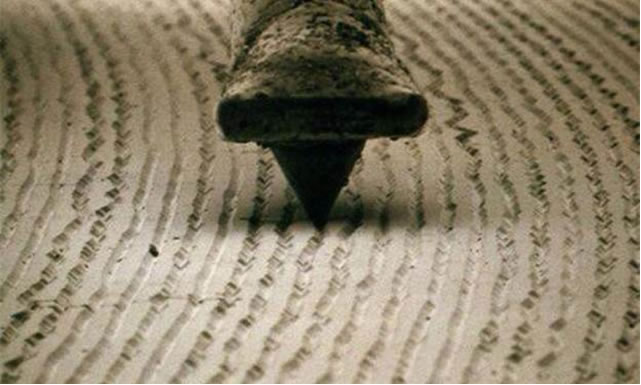 Close-up of a stylus and LP record
vinyl grooves
"Vinyl remains unsurpassed for
reproducing music, said Mark Döhmann, Founder of Döhmann Audio.
To convey vinyls rich, nuanced potential a turntable must have precise speed
control and operate without producing mechanical or electronic noise. The goal
is an uncompromised signal emerging from a silent background, resulting from
precisely designed construction that eliminates noise and gives precision speed
control for ideal playback.
This goal has been very closely
approximated with the release of the Helix One and Helix Two turntables,
representing a breakthrough in analog playback design and execution. These
turntables are a showcase for micro-signal architecture, a new way of thinking
borne from the world of ultra-precision sub-atomic research, where the removal
of unwanted vibration is critical to achieving precision results.
The
Helix One and Helix Two turntables reward the listener with the closest
facsimile to master tape yet realized. Their specifications demand the ultimate
in noise suppression and vibration isolation systems, allowing the turntables
and pick-up arms to deliver the micro-signals buried in the vinyl grooves of
LPs.
Every aspect of the turntables' design requires the preservation
of the micro-signals found in the grooves of the LP to be retrieved with as
little modification and distortion as physically and electronically possible,
added Döhmann. The turntables incorporate a number of engineering advances
to deliver the lowest resonance profile for any pickup arm and LP
combination.
These engineering advances include: a) mechanical crossover
technology; b) a tri-modal platter system; c) an edge-damping ring; d) a tone
arm damping system; e) resonance-tuned suspension; f) a diamond-like coating,
amorphous material-bearing friction modifier; g) high-torque, adjustable-drive
speed selections; and h) a velocity adjustment lock.
But what
contributes to making the Helix One and Helix Two turntables truly unique is
their highly precise, fully-integrated vibration isolation system.
The Need For Vibration
Isolation Vibration isolation in the playback process of high-end audio
systems is crucial. Any external vibration, no matter how slight, even someone
walking near the turntable or vibration from floor-mounted speakers, is sensed
by the turntables stylus and affects the sound being played back from the
record. Capacitors, resistors, transistors, tube amplifiers and other
electronic components are likewise sensitive to vibration.
Analog audio
is a very detailed and information rich storage and retrieval mechanism,
continued Döhmann. The enemy of retrieval information is vibration, which
can modulate with the needle as it works its way through the groove. If you can
remove exterior vibration and allow the needle to operate in an optimally quiet
method or platform, then you will get more information out because your noise
is much lower.
Full article...
More at our Audio & Turntable Vibration Isolation
Applications page... |
(2016 Legacy Article) The tunable
microwave-frequency alternating current scanning tunneling microscope (ACSTM)
has opened the possibility of recording local spectra and local chemical
information on insulator surfaces, much like the conventional scanning
tunneling microscope (STM) has done for metals and
semiconductors..
Spectroscopy in the microwave frequency range enables
unrealizable measurements on conducting substrates, such as the rotational
spectroscopy of a single adsorbed molecule. Developed in the early 1990s by
Professor Paul Weiss, the nano-pioneering Director of the Weiss Group, a
nanotechnology research unit of UCLAs California NanoSystems Institute, the
ACSTMs single-molecule measurement techniques have illuminated unprecedented
details of chemical behavior, including observations of the motion of a single
molecule on a surface, and even the vibration of a single bond within a
molecule. Such measurements are critical to understanding entities ranging from
single atoms to the most complex protein assemblies.We use molecular design,
tailored syntheses, intermolecular interactions and selective chemistry to
direct molecules into desired positions to create nanostructures, to connect
functional molecules to the outside world, and to serve as test structures for
measuring single or bundled molecules, said David McMillan, Lead Technician at
the Weiss Group.
Critical to understanding these variations has been
developing the means to make tens- to hundreds-of-thousands of independent
single-molecule measurements in order to develop sufficiently significant
statistical distributions, while retaining the heterogeneity inherent in the
measurements.
Vibration isolation To achieve
these nano-level chemical and spectroscopic data sets, the ACSTM must be
positioned in an ultra-stable operating environment, one free of low-frequency
vibrations.The lab was using almost exclusively optical tables on pneumatic
isolation, said McMillan.One of our big problems has been space constraint. We
needed smaller pneumatic optical tables to fit. But as the air tables get
smaller, their vibration isolation performance diminishes.
Full article... |
The compound microscope has evolved from an
instrument providing simple contrast viewing, into super-resolution systems
capable of sub-diffraction accuracy. Its two platforms, upright and inverted,
can be found in most laboratories doing cellular research, such as in biotech
and pharmaceutical. Upright microscopes are used for viewing glass slides, and
inverted for viewing live cells in Petri dishes. Despite its imaging advances,
the basic architecture of the compound microscope has not substantially been
modified in centuries.
This has now changed, with the recent release of
the Revolve hybrid compound microscope, developed by Echo Laboratories (Echo),
which has set a new precedent in microscope usability and design. The Revolve
combines the full functionality of both upright and inverted microscopes in one
instrument, and can switch between the two imaging modes relatively swiftly and
easily. This gives the flexibility to view many types of samples with one
microscope to a level of 300 350 nanometers resolution.
More than 70 percent of labs end up
having both inverted and upright microscopes, said Jeff Huber, Director
of Sales for Echo Laboratories. But both uprights and inverts use similar
objectives, illuminators, position systems and cameras. Why duplicate all of
these expensive components? And why take up valuable lab space with two
instruments? So, Echo Laboratories engineered a way to merge these two systems
into one unified instrument, which is the Revolve
microscope.
Brightfield, Phase Contrast and Epifluorescence
Imaging with iPad and Wireless Upload his is a compound, infinity-path
microscope, with applications for brightfield, phase contrast, and
epi-fluorescence imaging. Current glass selection includes the entire line of
Olympus objectives. Due to the unique nature of the upright/inverted
combination, both a high-NA and long-working-distance transmitted-light
condensers are available to support phase and brightfield. A high-accuracy
locking mechanism is used to securely hold the condenser assembly in place,
while still allowing for easy removal by a single lever.
Full article... |
Since the release of the first commercial
atomic force microscope (AFM) about 30 years ago, technology advances have
steadily been implemented to improve their performance. Now, the most recent
advance in ambient-temperature AFMs is making them more compact, portable and
user-friendly, which is enabled by Negative-Stiffness vibration isolation.
The atomic force microscope (AFM) has become one of the foremost tools
for imaging and measuring materials and cells on the nanoscale. Revealing
sample details at the atomic level, with resolution on the order of fractions
of a nanometer, the AFM is instrumental for imaging an array of applications,
such as defining surface characterizations, lithography, data storage, and
manipulation of atoms and nano-sized structures on a variety of
surfaces.
The AFM utilizes a sharp tip (probe) with a radius of
curvature on the order of a few nanometers attached to the end of a tiny
cantilever used to scan across a sample surface to image its topography and
material properties. When the tip is brought into proximity of a sample
surface, forces between the tip and the surface lead to a deflection of the
cantilever. This deflection is recorded using, typically, a laser beam that is
reflected from the top surface of the cantilever to a photo-sensitive detector.
The resultant change of position of the cantilever/probe/tip permits
characteristics such as mechanical, electrostatic, magnetic, chemical and other
forces to be precisely measured by the AFM. These characteristics are displayed
in a three-dimensional surface profile of the sample (in the X, Y and Z axes),
an advantage that the AFM can provide compared to other microscopy
techniques.
Although AFM technology has advanced considerably, its
benefits have not always been easily accessible for researchers requiring AFM
adaptability, portability. Nor have AFMs been adequately accessible in
nanotechnology student laboratories, because of lack of student skill in their
operation, and budget limitations on the number of AFMs at their
disposal.
A More Portable, More User-Friendly
AFM These inhibitions have now been mitigated by a relatively new
compact, portable and user-friendly ambient-temperature AFM. Developed by
NanoMagnetics Instruments, a leading manufacturer of scanning probe microscopes
for low-temperature applications, the ezAFM+ atomic force microscope is a
benchtop instrument designed for short learning times, quick setup, and ease of
transport.
Full article... |
BioOptics Vibration
Isolation | A Tool for Brain Discovery The ability to measure micron-level
neuronal activity patterns in the mammalian neocortex is enabling insight into
brain sensory and motor processing functions related to cardiac fibrillation
and epilepsy. Voltage-sensitive dye, optical recording techniques, and
vibration isolation are key to the work.
"At first, we used high-quality air
tables, but they were not adequate for isolating low frequency vibrations," but
then settled upon
negative-stiffness mechanism systems from
Minus K Technology. |
By Jim McMahon
(Legacy
Article) Professor Jian-Young Wu has been conducting research on waves of
neuronal activity in the neocortex of the brain. Wu and his colleagues at the
Department of Physiology and Biophysics at Georgetown University Medical Center
visualize wave-like patterns in the brain cortex using optical imaging and
voltage-sensitive dyea method that depends on robust vibration isolation. Their
neuronal specimens are derived from slices of rat neocortex, the outer layer of
a mammal's brain, which is involved in higher functions such as sensory
perception and generation of motor commands and, in humans, language.
The neurons of the neocortex are arranged
in vertical structures called neocortical columns that measure about 0.5 mm in
diameter and 2 mm in depth. Each column typically responds to a sensory
stimulus representing a certain body part, or region of sound or
vision.
In the human neocortex, it is postulated that there are about a
half-million of these columns, each of which contains approximately 60,000
neurons.
The neocortex can be viewed as a huge web, consisting of
billions to trillions of neurons and hundred of trillions of interconnections.
While individual neurons are too simple to have intelligence, the collective
behavior of the billions of interneuronal interactions occurring each second
can be highly intelligent.
Full article... |
Negative-stiffness
Minus K BM-8 vibration isolator beneath the
Neubrescope.
By Jim McMahon
The latest
generation of fiber optic sensing systems employed to monitor well conditions
can augment operational performance in the oil & gas industry. Critical
data about the downhole well environment from distributed fiber optic sensing
(DFOS) systems improves engineers and scientists ability to arrive at decisions
that support operational optimization. This leads to well production
performance enhancement and safety at the well site, with the ultimate goal of
optimizing production from oil and gas wells. There is no other current method
to acquire the quality and level of detail about physical conditions in a
wellbore compared to fiber optics.
Distributed acoustic sensing (DAS) is
mainly used to listen to hydraulic fracturing related signals, fluid and gas
flow signals, or to sense seismic source response, such as in a vertical
seismic profile (VSP). DAS senses changes in small physical acoustic vibrations
along a glass fiber optic strand encased in a cable to measure vibrations.
There are thousands of detection points along the fiber in the subsurface fiber
optic cable.
DFOS is a technology that enables continuous, real-time
measurements along the entire length of a fiber optic cable at minimal spatial
intervals. Unlike conventional sensor systems that rely on discrete sensors
measuring at pre-determined points, distributed sensing does not rely upon
manufactured, discrete sensors, but uses the optical fiber itself as both
sensing device and two-way transmitter of the signal (light). Optical fiber is
the sensing element. without any additional transducers in the optical path.
Surface instruments called interrogator units (IU) send a series of laser light
pulses into the fiber and records the return of the naturally occurring
back-scattered light signal as a function of time. In doing this, the
distributed sensing system measures at all points along the fiber which are at
a pre-determined clock-time interval over periods of well operational
time
Because fiber optic cable can be installed in harsh environments
for long periods of time, the technology holds promise for environmental
monitoring of sensitive geologic operations. Many geofluid systems require
dynamic acoustic, temperature, strain and pressure monitoring at great
pressure, depth and temperature. Sensors that employ fiber optic cables serve
well for such deployments because they can withstand adverse environments.
Downhole application includes oil and gas wells (hydraulic fracture completion
operations, flow-back operations, long-term well monitoring, and well-integrity
monitoring), geothermal wells, deep industrial waste disposal wells and other
harsh environment applications.
Neubrescope set up on site near well
operations.
Full article... |
Press Release: New Ultra-Thin
CT-2 Low-Frequency Vibration
Isolation Platform Adapts to Space Constraints in Critical Micro- and
Nano-Microscopy (replaces the CT-1)
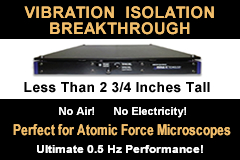

Full
release... |
|
|
|
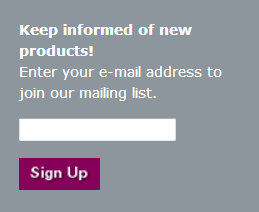
 |
|
|