|
Newsletter June 2022 | Menu of Newsletters
|
Give us your Challenge
|
Pricing |
Get a Quote |
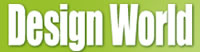
NASA's ICESat-2 Spacecraft relies
with testing using Minus K vibration isolation Inside a thermal vacuum chamber. No
electrical cords required.
|
NASAS Ice, Cloud and Land Elevation
Satellite-2 (ICESat-2), which lifted off three years ago, has generated a
comprehensive portrait of the complexities of ice sheet change and insights
into the future of Greenland and Antarctica. The ICESat-2 measurements, when
compared to the measurements taken by the original ICESat from 2003 to 2009,
showed that in Antarctica the ice sheet is getting thicker in parts of the
continent's interior, likely as a result of increased snowfall. But the massive
loss of ice from the continent's margins (due to ocean warming) far outweighs
any small gains in the interior.
|
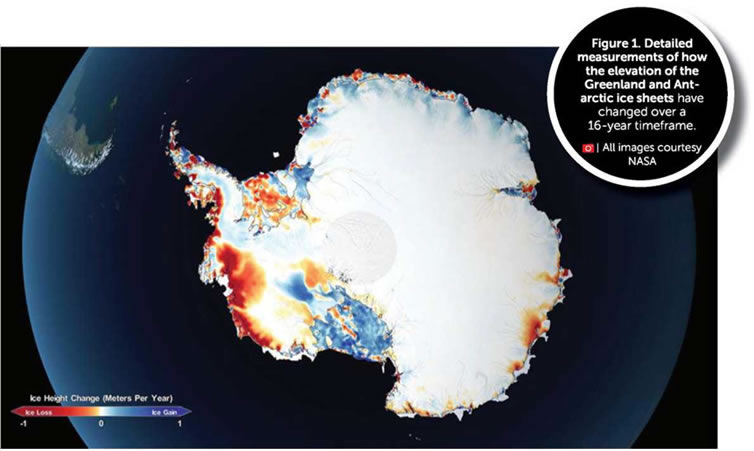
ICESat-2 will measure ice
heights in the polar regions
"The new analysis reveals the ice sheets'
response to changes in climate with unprecedented detail, revealing clues as to
why and how the ice sheets are reacting the way they are," said Alex Gardner, a
glaciologist at NASA's Jet Propulsion Laboratory."
This is one of the
first times that researchers have used laser altimetry to measure loss of the
floating ice shelves around Antarctica simultaneously with loss of the
continent's ice sheet. The researchers found ice shelves are losing mass in
West Antarctica, where many of the continent's fastest-moving glaciers are
located. Patterns of thinning over the ice shelves in West Antarctica show that
Thwaites and Crosson ice shelves have thinned the most, an average of about
16-ft and 10-ft of ice per year, respectively.
In this technique, AFM
tips or sharp needles can be employed to transfer small, femtoliter volumes of
molecular solutions, or other liquid-based ink, to predefined locations on the
surface of samples.
|
The vacuum chamber was configured with four
vacuum compatible Minus K 800CM-1CV negative-stiffness vibration
isolators to support the ATLAS instrument for the thermal vacuum testing. "The
Minus K isolators' primary use was inside the thermal chambers which did not
have as stable of a mounting surface as we would have liked," said Brian
Simpson, mechanical lead for ATLAS testing. "The isolators were critical in
cancelling out jitter introduced into our system by the facility."
Full article...
|
|
|
Compact CM-1 Low Frequency
Vibration Isolator
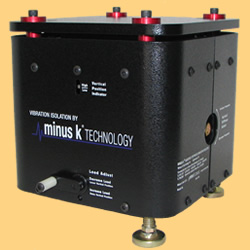
The
CM-1: is a
compact high capacity, low-frequency negative-stiffness isolator. As with all
Minus K isolators, they are completely passive and use no air or electricity.
The isolators can be combined into multi isolator systems to support heavy
payloads while taking up very little room themselves.
- Dimensions: 7.875" W x 7.875" D x 8.5" H (200mm W x
200mm D x 216mm H)
- Vertical natural frequency of 1/2 Hz or less can be
achieved over the entire load range.
- Horizontal natural frequency is load dependent. 1/2 Hz
or less can be achieved at or near the nominal load.
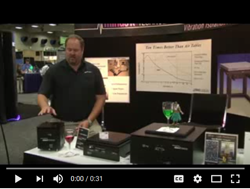 CM-1
Video
More...
Pricing & sizes for
CM-1
Specifications
(pdf) |
|
Give us your Challenge
|
Pricing |
Get a Quote |
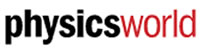
Sunken Treasure (2000 year old
Ancient Roman lead ingots) Surrounding The Coldest Cubic Meter In The
Universe Suspension of the cryostat uses
three Minus K Negative-Stiffness vibration isolators
Case Study |
November 2017 Legacy Article: The
Cryogenic Underground Observatory for Rare Events (CUORE) is a 1-ton scale
bolometric experiment that will examine a property of ghostly neutrinos by
looking for a phenomenon called neutrinoless double beta decay. Revealing this
process could be a clue as to why there is more matter than antimatter in the
universe and show that neutrinos get their mass in a way thats different from
all other particles.
Unlike ordinary beta decays, in which electrons and
antineutrinos share energy, the neutrinoless double beta decay produces two
electrons, but no neutrinos at all. It is as if the two antineutrinos that
should have been produced annihilate one another inside the nucleus.
|
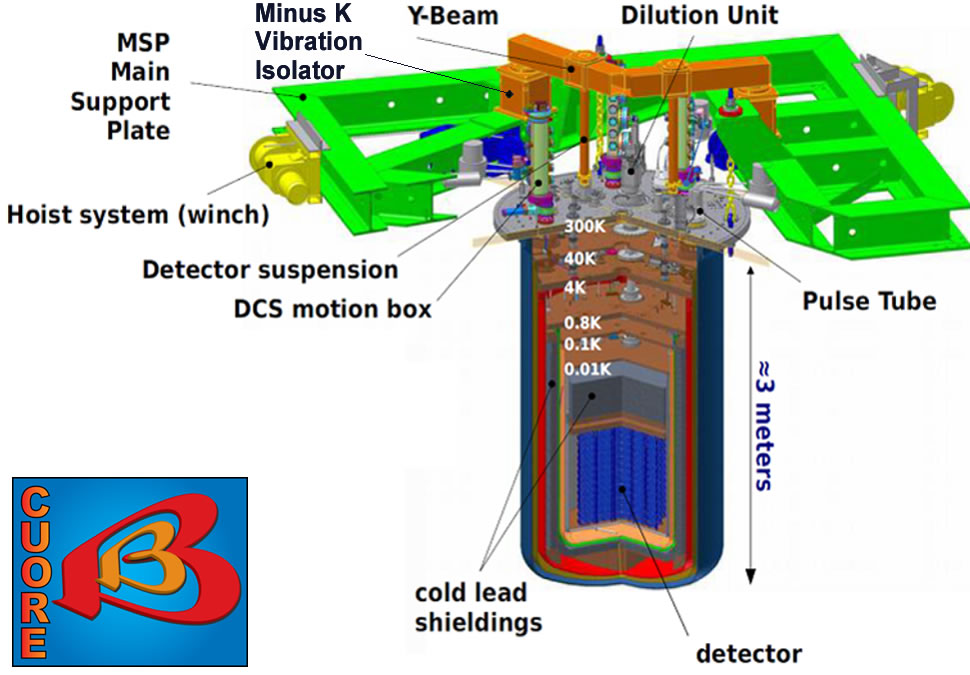
The Cryogenic Underground
Observatory Cryostat
The cryostat consists of six nested vessels and
shields. The three outermost ones are included in the outer Cryostat. Two of
them (300 K and 4 K) are vacuum tight: the space between the 300 K and 4 K
vessels constitutes the Outer Vacuum Chamber (OVC) of the cryostat and the 300
K vessel operates at room temperature. The volume inside the 4 K vessel
represents the Inner Vacuum Chamber (IVC) and in normal running condition this
vessel is thermalized to 4 K. Between the 300 K and 4 K vessel there is a
thermal radiation shield at 40 K covered with a multi-layer aluminized
superinsulation.
The entire cryostat is suspended from a heavy steel
support structure, Main Support Plate (MSP) which bears the load of close to 20
tons, specifically the detector (~1 ton), thermal shields and flanges (~8 tons)
and the internal lead shielding (~10 tons).
The detector suspension has
been designed to minimize the transmission of mechanical vibrations both due to
seismic noise and to the operation of cryocoolers and pumps. The suspension is
a two stage low-frequency isolator fixed to a Y-beam above the cryostat, in the
vertical direction, and a pendulum with a natural frequency of about 0.4Hz, in
the horizontal direction. It must provide load path for the detector while
minimizing the heat input and the vibration transmission.
The suspension
is made up of three Minus K Negative-Stiffness vibration isolators and
the Y-beam positioned on top of them which is mounted on top of the Main
Support Plate (MSP). The detector is suspended by the Ybeam through three
composite rods. The system formed by the Minus K isolators and the rest of the
detector will behave like a spring-mass system with a cut-off frequency of
0.5Hz. The composite rods are be made of several 316LN stainless steel rods,
with three copper thermal links connecting to 40K, 4K and Still plates. Also to
minimize vibrational noise of the detector as much as possible there are
independent suspensions for the vessels, dilution unit, and detector.
|
|
|
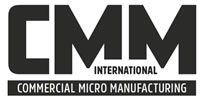
University of California
Merced Relies on Negative Stiffness Vibration Isolator from Minus K
Technology For
accurate research into microscale friction
Case Study |
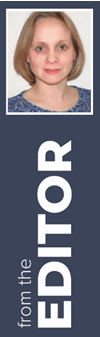 | |
Feb.2022 -- Elizabeth Valero, Editor CMM
Magazine: Welcome to the first issue of 2022, which, it goes without
saying, we all hope will be a significantly more positive year than the
previous two. CMM has got off to a good start, with articles expected from new
as well as old faces in the coming months, and I like to think this Is a sign
of our continuance on the road back to normality.
First I thought I
might highlight a case study on how a negative-stiffness vibration isolator
from Minus-K Technology has enabled the School of Engineering at the University
of California Merced (UC Merced) to isolate environmental vibrations and thus
obtain precision microscale or, more specifically, micronewton friction
measurements The school has been using a linear-reciprocating microtribometer
to conduct valuable research into friction and wear on different material
surfaces subjected to various loading and sliding speed conditions. In order to
acquire measurements at (he micron level the microtribometer needs to be
isolated from environmental vibrations, particularly very low hertz vibrations,
these can be due to many factors from equipment and people inside the building
to vehicles and construction noise outside of it.
The negative-stiffness
vibration isolator replaced the vibration isolator the school initially used
for its research but that proved inadequate. This is because the
microtribometer demanded greater vibration Isolation for the measurement of
friction in micronewtons. The ability of the negative-stiffness vibration
isolator 1o achieve a significantly higher level of vibration isolation means
The researchers can be confident that the friction response measured is
attributable to the microtribometer's sliding contact. Moreover, they are able
to study materials that have much lower frictions.
|
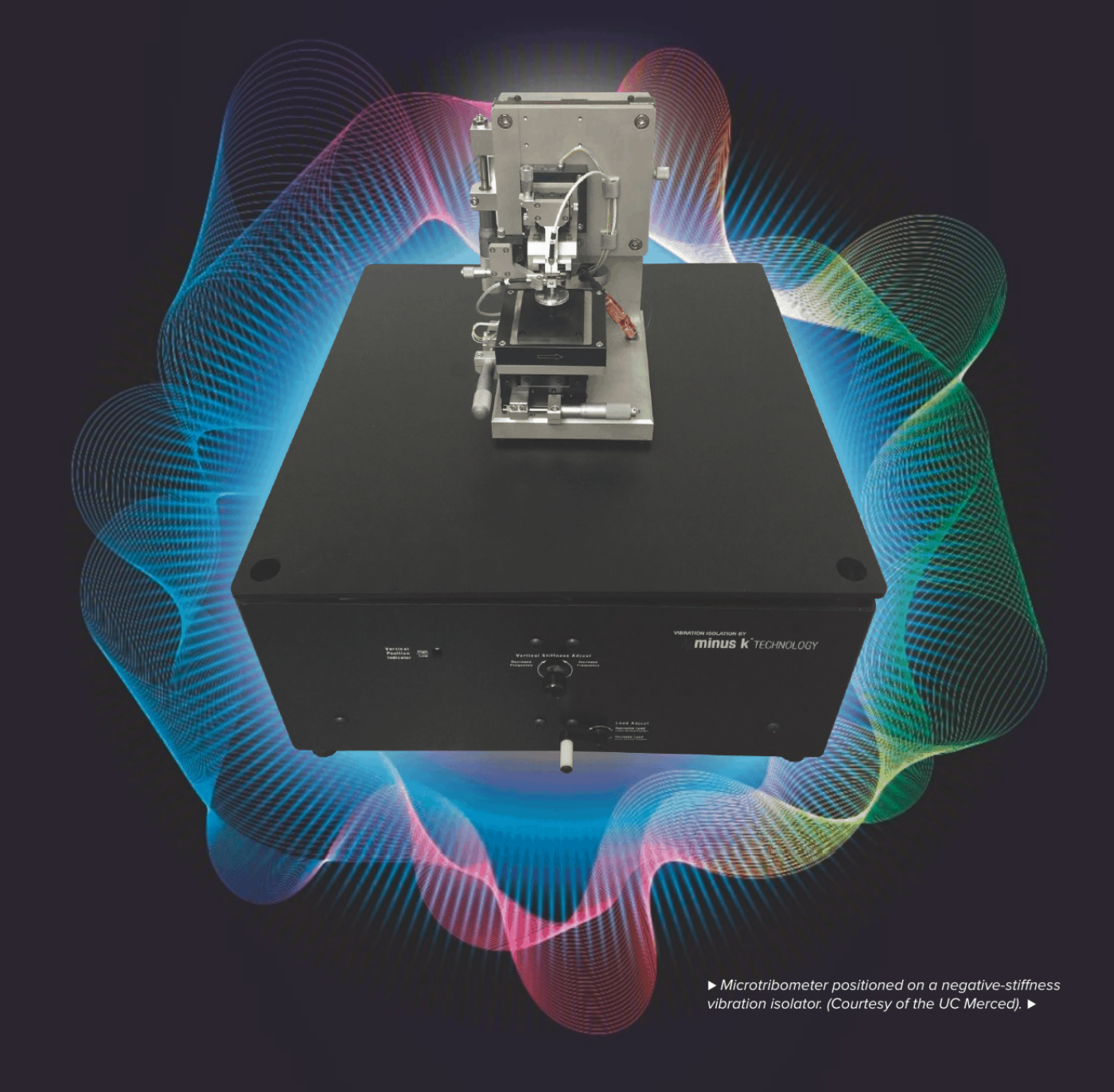
Microtribometer on a Miinus K
Negative Stiffness Vibration Isolator (Courtesy of the UC Merced)
The School of Engineering at the University of
California Merced (UC Merced) has been engaged In research focusing on
applications of microscale friction measurements to better understand
fundamental mechanisms underlying tribological phenomena. A critical end
fundamental component of the school's research Is the Isolation of
environmental vibrations utilizing a negative-stiffness vibration isolator from
Minus K Technology which has enabled precision measurements of friction at
micronewton magnitudes.
Whenever two surfaces are moving in contact with
each other their behavior is influenced by friction. Smooth surfaces, even
those polished lo a mirror finish, are not truly smooth on scales. They are
rough, with sharp or rugged projections referred to as
asperities.
Initially, the surfaces only touch at a few of these
asperity points which cover only a very small portion of the surface area.
Friction and wear originate at these points, so understanding their behavior
becomes important when studying materials in contact.
The measurement of
this fractional force between two surfaces is undertaken using a
microtriborneter This instrument measures quantities, such as coefficient of
friction and friction force between the two surfaces that are in contact These
measurements can relate to a number of types of important properties of
mechanical components, including energy efficiency.
The basic operation
of a microtribometer involves a flat of spherical surface that is moved
repetitively across the face of another material. An exact load is applied to
the moving part for the duration of the test. Equipment and methods used to
examine the surfaces before and after sliding include optical microscopes,
scanning electron microscopes, optical interferometers and mechanical roughness
testers. The final measurements show the wear on the material end are often
used to determine its strength and longevity.
The need for vibration
isolation Microtribometer measurements at the micron level require
isolation from ambient environmental vibrations, particularly very low hertz
vibrations. Isolating a laboratory s sensitive instrumentation against
low-frequency vibrations has become increasingly more vital to maintaining
imaging quality and data Integrity. |
|
|
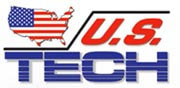
Negative-Stiffness Vibration
Isolation Aids Quantum Electronic Research
Single-Atom Flakes &
Quantum Electronics Vibration Isolation |
Better understanding the character and properties
of graphene, and similar two-dimensional materials, will advance their
integration into improvements for semiconductors, electronics, photovoltaics,
battery energy storage and many other applications.
One university laboratory that has been
conducting research with graphene and other atomically-thin materials for some
years is the Henriksen Research Group at Washington University in St. Louis,
Missouri.
Our experiments entail the careful measurement of the
electronic properties of thinly-layered materials, including both electronic
transport and thermodynamic quantities, such as the magnetization and
compressibility of electron gas, says Professor Erik Henriksen Ph.D., leading
professor of the Henriksen Research Group. We also conduct measurements of the
infrared absorption spectrum to probe the electronic structure directly.
The group searches for unusual and unexpected properties of
low-dimensional materials, utilizing a combination of electronic, optical and
thermodynamic measurement approaches to understand the novel quantum electronic
phases that arise. The experiments are generally conducted at very low
temperatures, fractions of a degree Kelvin above absolute zero, and in high
magnetic fields, employing custom devices made of graphene or related
crystals.
Single-Atom Flakes We look at the physics of the
layered graphene, where the layers are weakly bound, so they can be pulled
apart, explains Henriksen. We isolate these very thin layers down to a single
atom. Then, lift the graphene flakes from bulk graphite with adhesive tape,
transferring them very carefully onto silicon wafers.
Full article...
|
|
In its continuing efforts to revolutionize
discovery-based research into complex biological systems, Pacific Biosciences
has released its next generation of automated, long-read genomic sequencer with
single molecule, real-time (SMRT) sequencing technology the Sequel
System.
In its continuing efforts to revolutionize
discovery-based research into complex biological systems, Pacific Biosciences
has released its next generation of automated, long-read genomic sequencer with
single molecule, real-time (SMRT) sequencing technology the Sequel
System.
The Sequel System is very multifaceted in operation, says Kevin
Lin, mechanical engineer at Pacific Biosciences. It encompasses robotics,
chemical and biological processing, and photonics. Because its intended to be
used in diverse settings within research and laboratory environments, excessive
ambient vibrations could negatively influence the data sets. So, we needed to
implement a vibration isolation component that not only isolated the sensitive
components from vibrations, but also was sufficiently small, compact, and
integrative.
Internal and external factors can create vibration issues
from buildings housing the system including heating and ventilation systems,
fans, pumps, elevators, adjacent road traffic, nearby construction, loud noise
from aircraft, and weather conditions. These influences cause vibrations as low
as 2Hz that can create strong disturbances in sensitive equipment.
With
our earlier sequencer model, we used air tables for vibration isolation, which,
for the most part, performed adequately, Lin says. But use of the Sequel System
in more diverse locations, where low-frequency vibrations may be present to a
greater or lesser degree, necessitated a vibration isolator that was compact
enough to fit into our much smaller Sequel System and could effectively cancel
out these low-frequency vibrations.
Negative-stiffness vibration
isolation Pacific Biosciences ultimately decided on negative-stiffness
isolation to address their needs. Developed by Minus K Technology,
negative-stiffness isolators use completely passive mechanical technology for
low-frequency vibration isolation without using motors, pumps, or chambers,
making them zero maintenance. Because of their very high vibration isolation
efficiencies, particularly in the low frequencies, negative-stiffness vibration
isolation systems enable vibration- sensitive instruments, such as the Sequel
System, to operate in severe low-vibration environments that wouldnt be
practical with top-performance air tables and other vibration-mitigation
technologies...
Full article...
|
|
MInus K's Assist with the
Building of the JWST Telescope |
All of the JWST systems-level cryogenic vacuum
tests were performed at the NASA Johnson Space Centers (JSC) Chamber-A.
It is now the largest high-vacuum, cryogenic-optical test chamber in the
world, and made famous for testing the space capsules for NASA's Apollo
mission, with and without the mission crew. It is 55 feet (16.8 meters) in
diameter by 90 feet (27.4 meters) tall. The door weighs 40 tons and is opened
and closed hydraulically. The air in the chamber weighs 25 tons, when all the
air is removed the mass left inside will be the equivalent of half of a staple.
Diagram of the Cyrogenic Chamber in which the JWST
was tested for space.
For three years, NASA JSC engineers built and
remodeled the chambers interior for the temperature needed to test the James
Webb Space Telescope. Chamber A was retrofitted with the helium shroud, inboard
of the existing liquid-nitrogen shroud and is capable of dropping the chambers
temperature farther down than ever, which is 11 degrees above absolute zero (11
Kelvin, -439.9 Fahrenheit or -262.1 Celsius).
A key addition to Chamber
A was the addition of a set of six custom Minus K negative-stiffness
vibration isolators. The Minus K passive isolators do not require air and
offer better isolation than air and active isolation systems. A major factor in
the selection of the of the vibration isolators was that they not only isolate
vibration vertically, but also horizontally at less than 1 Hz.
JWST was
designed to work in space where the disturbances are highly controlled and only
come from the spacecraft, while on Earth with all the ground-based
disturbances, such as the pumps and motors, and even traffic driving by can
affect the testing. The Minus K vibration isolators provided dynamic isolation
from external vibration sources to create a near flight-like disturbance
environment.
The isolators utilize Minus K's patented Thermal
Responsive Element (TRE) compensator device, a passive mechanical device,
requiring no air or electricity just like the isolators. The TRE compensator
adjusted the isolators as the temperature changes throughout the testing at
JSC, keeping the JWST in the proper position.
The Critical Design Review
for Spacecraft-to-Optical Telescope Element vibration isolation system was
completed one month earlier than scheduled at the end of 2011. The six Minus K
negative-stiffness vibration isolators were installed on top of Johnson Space
Centers Thermal Vacuum Chamber A in March 2014.
JWST needed a support
structure inside the vacuum chamber to hold equipment for the testing.
Engineers installed a massive steel platform suspended from the six vibration
isolators via steel rods about 60 feet long (18.2 meters) each and about 1.5
inches (or 38.1 mm) in diameter, to hold the telescope and key pieces of test
equipment. The sophisticated optical telescope test equipment included an
interferometer, auto-collimating flat mirrors, and a system of photogrammetry
precision surveying cameras in precise relative alignment inside the chamber
while isolated from any sources of vibration, such as the flow of nitrogen and
helium inside the shroud plumbing and the rhythmic pulsing of vacuum
pumps.
Minus K's Involvement
continued...
-How much
farther can JWST see than the Hubble? -Why was
it launched from near the equator? -How cold
does the JWST get in space? -How did
origami play into the trip? -Why
24-karat gold on the mirrors?
Full article...
|
|
Our 29th
Anniversary is on 2/1/22 See the Milestones & Timeline
1993-2022
 | Founded in
1993 |  |
|
Minus
K Technology Opens 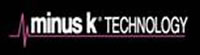
| |
Minus
K Technology opens for business in February 1993 |
Minus K's original SM-1 patented
Negative-Stiffness passive vibration isolator. This was the first commercialy
available vibration isolator offering 0.5 Hz natural frequencies for both
vertically and horizontally. This was accomplished without the use of air
compressors, computer componets or electricity.
The isolator could be used alone, or in conjunction with other units, and
could be engineered directly into a system. | |
Original
SM-1 Vibration Isolator
|
Our 29th
Anniversary is on 2/1/22 See the Milestones & Timeline
1993-2022
Within Saint Louis Universitys (SLU)
Department of Physics, research has been ongoing in the development of novel
techniques for synthesis, characterization and measurement of low dimensional
(1D and 2D) systems. This is in hopes to better understand how size, geometry
or interfacing various materials and nanostructures influences the properties
of the resulting systems.
Nanolithography Research
Nanolithography in general terms is concerned with the study and
application of fabricating nanometer-scale structures, meaning patterns with at
least one lateral dimension between 1 and 100 nm. A prime focus is very
largescale integration (VLSI) and ultralarge-scale integration (ULSI)
technology of nanoelectromechanical (NEMS) systems, and the need for better
atomic-scale understanding of issues arising from the miniaturization of
silicon devices. Under the direction of Dr. Irma Kuljanishvili, who heads up
SLUs nanomaterials and nanofabrication research lab, the groups focus is on
This approach is similar to a technique known as dip pen
nanolithography.
In this technique, AFM tips or sharp needles can be
employed to transfer small, femtoliter volumes of molecular solutions, or other
liquid-based ink, to predefined locations on the surface of
samples.
Carbon nanotubes, grapheme and other atomically monolayered
materials are being considered as prime candidates for nanoscale science and
technology applications, due to their unique and superior combination of
electrical, thermal, optical and mechanical properties, says
Kuljanishvili.
SLU's Negative-Stiffness Vibration Isolation
System
Full article...
|
|
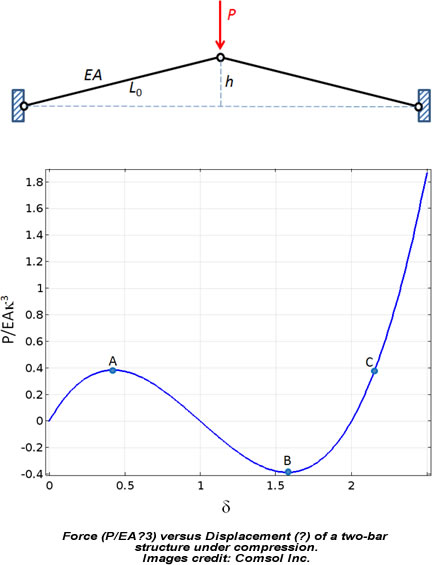
Notice that between points A and B, displacement is
increasing while force is decreasing. Thus, the structures stiffness is
negative in that region.
Negative-stiffness vibration isolators consist
of a horizontal isolator and a vertical isolator connected in series. To
counter motions that involve rotation (pitch and roll), a tilt motion pad can
also be connected in series with the horizontal and vertical isolators.
The horizontal isolator consists of two fixed-free vertical beams
(columns) supporting a weight. The weight imparts both eccentric (off-axis)
axial compressive load and a transverse bending load. This phenomenon is
referred to as the beam-column effect and causes the lateral bending stiffness
of the beams to decrease. In effect, the isolator is acting as a horizontal
spring with a negative-stiffness mechanism.
The horizontal isolator
is designed to take advantage of the beam-column effect, allowing it to act
like a negative-stiffness mechanism.
Vertical motion is addressed using two horizontal
flexures loaded in compression, which form a negative-stiffness mechanism. The
flexures are supported at their outer ends and connected to a stiff spring at
their inner ends. The stiffness of the isolator is determined by the design of
the flexures and by their compressive load.
Two flexures, fixed at their outer ends and
connected to a spring at their inner ends, form a negative-stiffness mechanism
that isolates equipment from vertical motion due to vibrations.
Full article...
|
|
Press Release:
New Ultra-Thin
CT-2 Low-Frequency
Vibration Isolation Platform Adapts to Space Constraints in Critical Micro-
and Nano-Microscopy (replaces the CT-1)
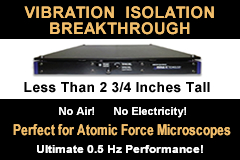

Full
release... |
|
|
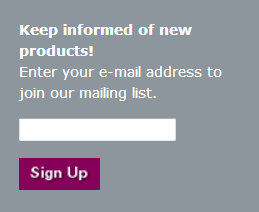
 |
|
|