|
Newsletter November 2022 | Menu of Newsletters
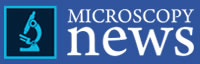 Microscopy News (Legacy Article
Aug2017)
Superionic Solid Electrolytes for Next-Generation Lithium
Batteries: Negative-Stiffness Vibration Isolation Facilitates
Nano-Research
Full article and larger
images...
Advances in materials testing techniques have enabled
scientists and engineers to measure mechanical properties, and observe and
characterize mechanical phenomena that control deformation and failure down to
nearly the atomic level. One field that is benefiting from such advances in
testing techniques is energy storage. The option of creating higher energy
capacity batteries has direct implications on
performance with
laptops, smartphones, and electric vehicles. Many of the
rechargeable batteries used in these portable devices and vehicles are
lithium-ion (Li-ion), composed of two electrodes, a positive electrode made of
lithium and a negative electrode made of graphite, and a chemical electrolyte.
The tremendous capacity of lithium and the metals ability to move lithium ions
and electrons in and out of an electrode as it cycles through charge and
discharge, make it a well suited anode material.
The electrolyte
chemically contains the electric charge and also acts as the medium through
which the current flows between electrodes when the battery is connected in a
circuit. As the electrolyte in a Li-ion battery also contains a solution of
lithium, the lithium electrode tends to react with this medium, causing
dendrite fibers to form over the course of battery charge and discharge cycles,
particularly when the battery is cycled at a fast rate. These fibers move out
from the electrode and into the electrolyte, where they break down the
controlled path that the electrons generally take by producing conductive paths
haphazardly throughout the structure. This can result in a rapid discharge that
allows excess current to flow,
causing the battery
to fail prematurely. It can also unsafely heat up the
battery to a point where it can generate fire.
To realize significant
improvements in energy density, vehicle range, cost requirements, and safety,
the use of metallic lithium anodes will likely be required for powerful
next-generation rechargeable battery chemistries like lithium-air and
lithium-sulfur. However, the use of metallic lithium with liquid and polymer
electrolytes is limited due to dendrite formation, and
efforts to solve this
problem have met with limited success.
Researching Pure
Lithium and Superionic Solid-State Electrolytes An
alternative approach is being pursued at Michigan Technical Universitys
Department of Materials Science and Engineering, Small-Scale Mechanical Testing
Laboratory, in collaboration with Oak Ridge National Laboratory and the
University of Michigan. The research focuses on a pure lithium anode accessed
through, and protected by a superionic solid-state electrolyte that would
prevent side reactions and enable safe, long-term, and high-rate cycling
performance.
Our lab is focused on the mechanical characterization
of small volumes of materials, said Erik G. Herbert PhD, Assistant Professor,
Department of Materials Science and Engineering, Michigan Technical University.
We are trying to understand how materials like metals, ceramics, polymers,
composites, and biomaterials respond when their boundaries are mechanically
loaded. We perform experiments relating to characteristics such as elasticity
and hardness, to probe the properties of these materials.
The key risk
and current limitation of Li-ion technology is the gradual loss of lithium over
the cycle life of the battery, said Dr. Herbert. In particular, losses caused
by physical isolation from roughening, dendrites or delamination processes, or
to chemical isolation from side reactions. To abate these problems we endeavor
towards a much deeper analysis of the degradation processes and a predictive
understanding of the lithium-metal solid electrolyte interface as a function of
cycling.
Specifically, we need to understand how the lithium is
gradually consumed, why the interfaces are surprisingly resistive, how the
electrolyte eventually fails, how defects in the lithium migrate, agglomerate
or anneal with further cycling or time, continued Dr. Herbert. And
additionally, whether softer electrolytes can be used without incursion of
lithium dendrites, and what effects processing and fabrication have on the
interface performance.
Among the efforts being pursued to answer these
questions,
state-of-the-art
small-scale mechanical characterization techniques are being
carried out at Michigan Technical University to provide the critical
information that will directly enable transformative insights into the complex
coupling between the microstructure, its defects and the mechanical behavior of
both lithium and the solid-state electrolytes.
Nanoindentation
Studies In addition to an extensive array of optical and
electron microscopes, atomic force microscopes and x-ray diffraction
instruments accessible through the universitys Applied Chemical and
Morphological Analysis Laboratory, the Small-Scale Mechanical Testing
Laboratory operates a versatile suite of six small-scale mechanical testing
platforms in which the user has direct control over the way the test is
performed and how the raw data are recorded, reduced, and analyzed...
Full
article...
|
Featured Product: BM-10 Bench Top Vibration Isolation
Platform
- Horizontal frequencies are weight dependent.
- Horizontal frequency of 1.5 Hz is achieved at the upper
limit of the payload range.
- At the lower limits of the payload range the horizontal
frequency is approximately 2.5 Hz.
- Vertical frequency is tunable to 0.5 Hz throughout the
payload range.
The
BM-10 bench top platform offers 10-100 times better
performance than a full size air table in a package only 4.6 inches tall and 12
inches wide and deep. It also does this without any air or
electricity!
This vibration isolation platform is extremely easy to use
and offers extreme performance. It offers a 1.5Hz horizontal natural frequency
and our signature 0.5 Hz vertical natural frequency.
There are only two
adjustments. The
BM-10 is perfect for new generations of small
SPM's that require the highest performance in a very compact
system.
This is the thinnest, smallest footprint, most portable, and
most user-friendly isolator ever offered that is capable of delivering this
level of performance.They can also be made cleanroom and vacuum
capatible.
Pricing & Specifications |
|
|
Give us your Challenge
|
Pricing |
Get a Quote |
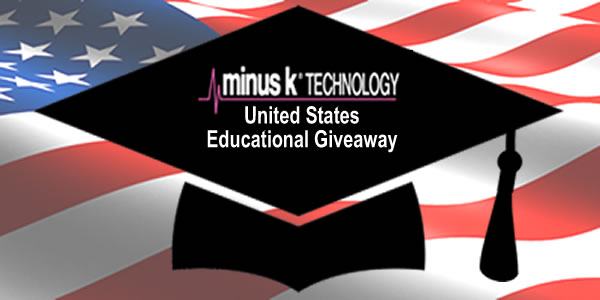
Announcing the 2020 Minus K
Technology Educational Giveaway to U.S. Colleges and
Universities
Minus K Technology, Inc. is giving away $25,000* worth
of patented vibration isolators to colleges within the United
States.
Your college could receive one of our superior performing
negative-stiffness low-frequency vibration isolators, which use no air or
electricity and are currently being used for biology, neuroscience, chemistry,
crystal growing, physics, audio reproduction and many other fields.
If
you have an Atomic Force Microscope (AFM), Electron Microscope, Interferometer,
Laser Optical System, Micro Hardness Tester, or any other special equipment
that would be assisted by our vibration isolation, simply complete the giveaway
submission form and send it back to edgiveaway@minusk.com. If you're one of the
top applicants, we'll send you one of these free vibration isolators to assist
you with your research.
more...
|
|
|
October 2018 Legacy Article: When built
into inspection equipment, like a coordinate measuring machine, a laser
interferometer system reports the surface condition of a product with more
accuracy than any other method. Such a precision laser-position measurement
system allows users to improve product quality and reliability, and increase
manufacturing consistency and production yields.
|
(High Resolution Microscopy Workstation,
Mounted on a Minus K Vibration Isolation Platform)
Micro- and nano-level microscopy, whether used in
academic laboratories or industry, is susceptible to vibrations from the
environment, requiring these instruments to employ vibration isolation systems.
When measuring a very few angstroms, nanometers, or microns of displacement, an
absolutely stable surface must be maintained to support the instrument. Any
vibrations that are transferred into the mechanical structure of the instrument
will cause vertical and horizontal noise, compromising data sets and limiting
the ability to measure high resolution features.
Traditionally, air
tables have been the isolators used for microscopy equipment. The ubiquitous
passive-system air tables, adequate up until a decade ago, are now being
seriously challenged by the need for more refined imaging requirements. Air
systems provide limited isolation vertically and very little isolation
horizontally. Yet, high-resolution microscopy demands vibration isolation
requirements that are unparalleled in both the vertical and horizontal axes.
This has posed a significant challenge for many researchers.
CENTER
FOR LEARNING AND MEMORY Such was the case with the Center for Learning
and Memory (CLM), part of the Department of Neuroscience at the University of
Texas at Austin, a multi-disciplinary group studying the mechanisms governing
the processes of learning and memory in animals.
Research in one of the
CLM laboratories is primarily directed to understanding the cellular and
molecular mechanisms of synaptic integration and long-term plasticity of
neurons in the animal medial temporal lobe. The lab focuses attention on the
hippocampus, subiculum, and prefrontal cortex areas of the brain that play
important roles in learning and memory. These regions are also of interest
because they have a low seizure threshold and are implicated in several forms
of human epilepsy
Neurons are electrically excitable cells that process
and transmit information through electrical and chemical signals in a process
known as neurotransmission, also called synaptic transmission. The fundamental
process that triggers the release of neurotransmitters is the action potential,
a propagating electrical signal that is generated by exploiting the
electrically excitable membrane of the neuron.
VIBRATION
PROBLEM... Full article...
|
|
|
|
November 2010 Legacy Article: Minus K
Technology's compact, high-capacity, low-frequency negative-stiffness isolator
is designed to support heavy payloads while reducing low-frequency vibrations.
The
LC-4 isolator comes in
several capacity ranges to match vibration-sensitive instruments for weight
loads from 1 to 130 lbs. The LC-4 comes in two versions (low-frequency
horizontal and ultra-low-frequency horizontal). Both versions can deliver a
vertical natural frequency of 0.5 Hz or less, which can be achieved over the
entire load range. Horizontal natural frequency is load dependent. The
low-frequency version has a 1.5-Hz natural frequency, while the
ultra-low-frequency version can achieve 0.5 Hz or less near the nominal
loads.
|
The need for precise vibration isolation with
scanning probe microscopy (SPM) and nearfield scanning optical microscopy
(NSOM) systems is becoming more critical as resolutions continue to bridge from
micro to nano. Whether used in academic labs or commercial facilities, SPM and
NSOM systems are extremely susceptible to vibrations from the environment.
When measuring a very few angstroms or nanometers of displacement,
an absolutely stable surface must be established for the instrument. Any
vibration coupled into the mechanical structure of the instrument will cause
vertical and/or horizontal noise and bring about a reduction in the ability to
measure high-resolution features. The vertical axis is the most sensitive
parameter for SPMs, but these instruments can also be quite sensitive to
vibrations in the horizontal axis. Lab design teams obviously need to
plan for these special equipment requirements, as they make decisions
regarding building-level isolation techniques and localized techniques.
Traditionally, bungee cords and high-performance air tables have been the
vibration isolators most used for SPM and NSOM work. The ubiquitous
passive-system air tables, adequate until a decade ago, are now being
challenged by the more refined imaging requirements. Bench-top air systems
provide limited isolation vertically and very little isolation horizontally.
Also at a disadvantage are active isolation systems, known as
electronic force cancellation, which use electronics to sense motion and then
implement equal amounts of motion electronically to compensate and cancel out
the motion. Active systems are somewhat adequate for applications with lasers
and optics, since they can start isolating as low as 0.7 Hz. But because they
run on electricity, they can be negatively influenced by problems of electronic
dysfunction and power modulations, which can interrupt scanning.
Lately, the introduction of integrated microscopy systems employing
multiple scopes is enabling more complex optical measurements, but these
systems are also much heavier, and there has been little vibration-isolation
technology available for such heavy instrumentation. Air tables, which have
been liberally used for optics applications, are not ideal for these nano-scale
resolution systems because of their inability to effectively isolate vibrations
below 20 Hz. Nor can active systems be used with these newer combination
systems because of their inability to handle heavy instrumentation.
Negative-stiffness mechanism (NSM)
vibration isolation offers a viable alternative choice for SPM
and NSOM systems. This includes applications using atomic force microscopy
(AFM) integrated with micro-Raman spectroscopy, where negative-stiffness
vibration isolation is particularly well-adapted. In fact, it is the
application of negative-stiffness isolation that has enabled AFMs to be truly
integrated with micro-Raman. Negative-stiffness isolators can handle the weight
of a combined system, as well as isolating the equipment from low-frequency
vibrations: a critical set of factors that high-performance air tables and
active systems cannot achieve. The neuronal sample is derived from slices of
rat neocortex.
|
|
|
|
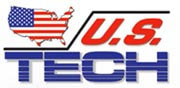
Negative-Stiffness Vibration
Isolation Aids Quantum Electronic Research
Single-Atom Flakes &
Quantum Electronics Vibration Isolation |
Better understanding the character and properties
of graphene, and similar two-dimensional materials, will advance their
integration into improvements for semiconductors, electronics, photovoltaics,
battery energy storage and many other applications.
One university laboratory that has been
conducting research with graphene and other atomically-thin materials for some
years is the Henriksen Research Group at Washington University in St. Louis,
Missouri.
Our experiments entail the careful measurement of the
electronic properties of thinly-layered materials, including both electronic
transport and thermodynamic quantities, such as the magnetization and
compressibility of electron gas, says Professor Erik Henriksen Ph.D., leading
professor of the Henriksen Research Group. We also conduct measurements of the
infrared absorption spectrum to probe the electronic structure directly.
The group searches for unusual and unexpected properties of
low-dimensional materials, utilizing a combination of electronic, optical and
thermodynamic measurement approaches to understand the novel quantum electronic
phases that arise. The experiments are generally conducted at very low
temperatures, fractions of a degree Kelvin above absolute zero, and in high
magnetic fields, employing custom devices made of graphene or related
crystals.
Single-Atom Flakes We look at the physics of the
layered graphene, where the layers are weakly bound, so they can be pulled
apart, explains Henriksen. We isolate these very thin layers down to a single
atom. Then, lift the graphene flakes from bulk graphite with adhesive tape,
transferring them very carefully onto silicon wafers.
Full article...
|
|
In its continuing efforts to revolutionize
discovery-based research into complex biological systems, Pacific Biosciences
has released its next generation of automated, long-read genomic sequencer with
single molecule, real-time (SMRT) sequencing technology – the Sequel
System.
In its continuing efforts to revolutionize
discovery-based research into complex biological systems, Pacific Biosciences
has released its next generation of automated, long-read genomic sequencer with
single molecule, real-time (SMRT) sequencing technology – the Sequel
System.
The Sequel System is very multifaceted in operation, says Kevin
Lin, mechanical engineer at Pacific Biosciences. It encompasses robotics,
chemical and biological processing, and photonics. Because its intended to be
used in diverse settings within research and laboratory environments, excessive
ambient vibrations could negatively influence the data sets. So, we needed to
implement a vibration isolation component that not only isolated the sensitive
components from vibrations, but also was sufficiently small, compact, and
integrative.
Internal and external factors can create vibration issues
from buildings housing the system including heating and ventilation systems,
fans, pumps, elevators, adjacent road traffic, nearby construction, loud noise
from aircraft, and weather conditions. These influences cause vibrations as low
as 2Hz that can create strong disturbances in sensitive equipment.
With
our earlier sequencer model, we used air tables for vibration isolation, which,
for the most part, performed adequately, Lin says. But use of the Sequel System
in more diverse locations, where low-frequency vibrations may be present to a
greater or lesser degree, necessitated a vibration isolator that was compact
enough to fit into our much smaller Sequel System and could effectively cancel
out these low-frequency vibrations.
Negative-stiffness vibration
isolation Pacific Biosciences ultimately decided on negative-stiffness
isolation to address their needs. Developed by Minus K Technology,
negative-stiffness isolators use completely passive mechanical technology for
low-frequency vibration isolation without using motors, pumps, or chambers,
making them zero maintenance. Because of their very high vibration isolation
efficiencies, particularly in the low frequencies, negative-stiffness vibration
isolation systems enable vibration- sensitive instruments, such as the Sequel
System, to operate in severe low-vibration environments that wouldnt be
practical with top-performance air tables and other vibration-mitigation
technologies...
Full article...
|
|
MInus K's Assist with the
Building of the JWST Telescope |
All of the JWST systems-level cryogenic vacuum
tests were performed at the NASA Johnson Space Center’s (JSC) Chamber-A.
It is now the largest high-vacuum, cryogenic-optical test chamber in the
world, and made famous for testing the space capsules for NASA's Apollo
mission, with and without the mission crew. It is 55 feet (16.8 meters) in
diameter by 90 feet (27.4 meters) tall. The door weighs 40 tons and is opened
and closed hydraulically. The air in the chamber weighs 25 tons, when all the
air is removed the mass left inside will be the equivalent of half of a staple.
Diagram of the Cyrogenic Chamber in which the JWST
was tested for space.
For three years, NASA JSC engineers built and
remodeled the chambers interior for the temperature needed to test the James
Webb Space Telescope. Chamber A was retrofitted with the helium shroud, inboard
of the existing liquid-nitrogen shroud and is capable of dropping the chambers
temperature farther down than ever, which is 11 degrees above absolute zero (11
Kelvin, -439.9 Fahrenheit or -262.1 Celsius).
A key addition to Chamber
A was the addition of a set of six custom Minus K negative-stiffness
vibration isolators. The Minus K passive isolators do not require air and
offer better isolation than air and active isolation systems. A major factor in
the selection of the of the vibration isolators was that they not only isolate
vibration vertically, but also horizontally at less than 1 Hz.
JWST was
designed to work in space where the disturbances are highly controlled and only
come from the spacecraft, while on Earth with all the ground-based
disturbances, such as the pumps and motors, and even traffic driving by can
affect the testing. The Minus K vibration isolators provided dynamic isolation
from external vibration sources to create a near flight-like disturbance
environment.
The isolators utilize Minus K's patented Thermal
Responsive Element (TRE) compensator device, a passive mechanical device,
requiring no air or electricity just like the isolators. The TRE compensator
adjusted the isolators as the temperature changes throughout the testing at
JSC, keeping the JWST in the proper position.
The Critical Design Review
for Spacecraft-to-Optical Telescope Element vibration isolation system was
completed one month earlier than scheduled at the end of 2011. The six Minus K
negative-stiffness vibration isolators were installed on top of Johnson Space
Centers Thermal Vacuum Chamber A in March 2014.
JWST needed a support
structure inside the vacuum chamber to hold equipment for the testing.
Engineers installed a massive steel platform suspended from the six vibration
isolators via steel rods about 60 feet long (18.2 meters) each and about 1.5
inches (or 38.1 mm) in diameter, to hold the telescope and key pieces of test
equipment. The sophisticated optical telescope test equipment included an
interferometer, auto-collimating flat mirrors, and a system of photogrammetry
precision surveying cameras in precise relative alignment inside the chamber
while isolated from any sources of vibration, such as the flow of nitrogen and
helium inside the shroud plumbing and the rhythmic pulsing of vacuum
pumps.
Minus K's Involvement
continued...
-How much
farther can JWST see than the Hubble? -Why was
it launched from near the equator? -How cold
does the JWST get in space? -How did
origami play into the trip? -Why
24-karat gold on the mirrors?
Full article...
|
|
Our 29th
Anniversary is on 2/1/22 See the Milestones & Timeline
1993-2022
Press Release:
New Ultra-Thin
CT-2 Low-Frequency
Vibration Isolation Platform Adapts to Space Constraints in Critical Micro-
and Nano-Microscopy (replaces the CT-1)
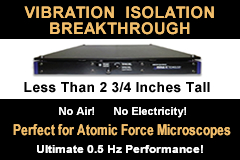

Full
release... |
|
|
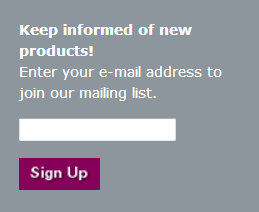
 |
|
|