|
Newsletter October 2024 | Menu of
Newsletters
|
|
NASAs Lunar Atmosphere and Dust
Environment Explorer (LADEE), pronounced Laddie, was a robotic mission
launched in 2013 that orbited the moon to gather detailed information about the
structure and composition of the thin lunar atmosphere, and the first-ever
Lunar Laser Communications Demonstration (LLCD). The LLCD used lasers, not
radio waves, like other spacecraft that have flown beyond close-Earth orbit
have used, to communicate with controllers on Earth allowing the spacecraft to
communicate at broadband speeds with the ground. |
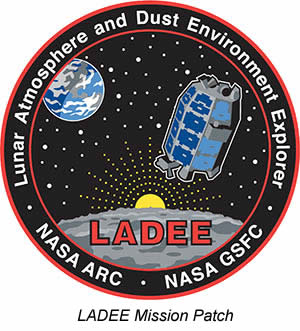 |
The probe was approximately
7.7ft x 4.75ft x 4.75ft, weighing 383kg (844 lb). The probe took about 30 days
to get to the moon. LADEE then went through a checkout period for another 30
days. After that, the probe conducted a 100-day science mission and was even
able to extend its mission for an additional month..
Once LADEEs mission
was completed, NASA intentionally impacted the probe into the far side of the
moon, away from historically important sites like the Apollo landing zones.
Lunar Laser Communications Demonstration The LLCD was a
project undertaken by MIT Lincoln Laboratory, NASA's Goddard Space Flight
Center, and the Jet Propulsion Laboratory. It was NASAs first attempt to
demonstrate optical communications between a lunar orbiting spacecraft and
Earth-based ground receivers.
|
|
All prior communications with spacecraft
beyond close-Earth orbits required spacecraft to have small, low-mass,
low-power radio transmitters and giant satellite dishes on Earth to receive
their messages. LLCD was an alternative process to replace traditional radio
communications with specialized lasers and laser detection units to send
information between lunar orbit and three receiving stations in the U.S. and
Spain.
LLCD demonstrated error-free communication from the moon,
including during broad daylight and even when the moon was within 3° of the
sun, as seen from Earth. LLCD also operated error-free when the moon was less
than 5° above the horizon, as seen from the ground station, which showed
that wind and atmospheric turbulence didnt significantly impact the system.
LLCD was even able to communicate through thin cirrus clouds.
The 30-day
test was a much more comprehensive check of its utility for all-purpose
communication. Rather than simply downloading a pre-arranged file, NASA used
the device for real communication with LADEE, and real collection of data.
While all LADEEs science data went to the ground via radio frequency (RF) link,
the data sent by the LLCD test was verified against the RF data, demonstrating
the feasibility of laser communication uplink/downlink for future
missions.
The LLCD used a pulsed laser beam to transmit data over the
239,000 miles from the moon to Earth at a record-breaking data-download speed
of 622 Megabits per second (Mbps), versus 75Mbps. This download speed was more
than 6x faster than the speed achieved by the best radio system ever flown to
the moon and would normally take several days to download.
LLCD also
demonstrated a 20Mbps uplink, which was used to loop back error-free
high-definition video to and from the moon, important for future human
exploration missions, and also provided simultaneous centimeter-class precision
ranging to the spacecraft, which can be used to improve the gravity models of
planetary bodies.
|
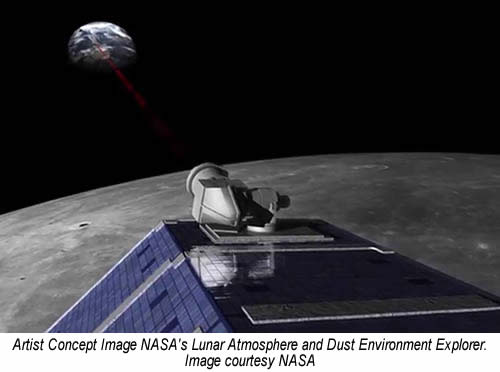 |
The testing looked at more than raw download
speed, prioritizing signal reliability and accuracy, along with possible
distance effects. LLCD worked well even at extremely oblique angles, when the
satellite was near the Earths horizon and its signals were forced to move
through the thickest portions of the atmosphere. The laser signal could be read
without error even in broad daylight and through light clouds.
In
addition to this lack of error, the LLCD was able to switch from one ground
station to the next as the Earth turned, in a manner that NASA compared to how
a mobile phone network operates, and the system did so without human
intervention. The system could even lock on to the ground stations without
using a radio signal.
The real breakthrough of the LLCD demonstration,
however, was the spectacular success of its essentially flawless operations,
allowing the system to return real, high-value science data from LADEEs
instruments investigating the moons environment and showing the promise of
laser communication for future missions.
The downside for the future is
range. Simply boosting power to the laser to make it cohere better over a
longer distance is a losing game. A more reasonable solution, and one NASA is
working toward, is the Lunar Communications Relay Demonstration (LCRD). This
would see NASA pepper space with laser-routers to read and re-transmit laser
signals from a new transmitter. LCRD is aboard the U.S. Department of Defenses
Space Test Program Satellite 6 (STPSat-6) launched December
2021.
Article
continued...
|
|
|
|
|
|
|
Only 2.7"
High The NEW
CT-10 Ultra-Thin Low-Height Tabletop Vibration Isolation
Platform
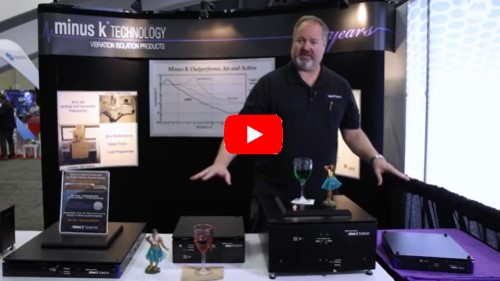
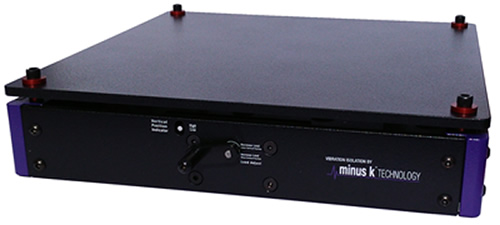
The Compact Tabletop
(CT-10)uses
Minus K's patented breakthrough technology allowing for the best performance on
the market in just a 2.7 inch tall; approximately 12.6 inches deep and wide
isolation platform. This unit is as tall as Minus K's CT-2 and offers similar
horizontal performance with additional payload ranges for smaller
instruments..
This completely passive mechanical isolator offers 10-100
times better performance than a full size air table. It does this without any
air or electricity!
This vibration isolation platform is extremely easy
to use and offers our signature 0.5 Hz vertical natural frequency and ~1.5 Hz
horizontal natural frequency. There are only two adjustments. The
CT-10
is ideal for all types of benchtop microscopes
This is the thinnest,
most portable and most user-friendly isolator ever offered that is capable of
delivering this performance.
See
Weight & Pricing Details...
|
|
|
|
|
|
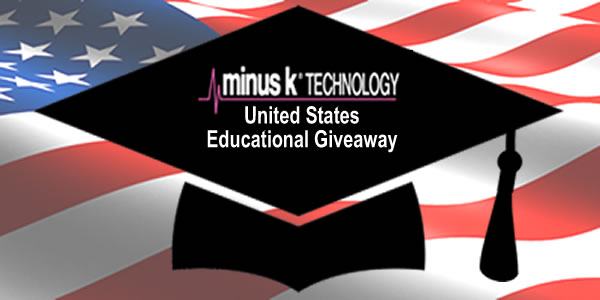
Announcing
the 2025 Minus K Technology Educational $25,000 Giveaway to U.S. Colleges
and Universities
Minus K
Technology, Inc. is giving away $25,000* worth of patented vibration
isolators to colleges within the United States.
Your college could
receive one of our superior performing negative-stiffness low-frequency
vibration isolators, which use no air or electricity and are currently being
used for biology, neuroscience, chemistry, crystal growing, physics, audio
reproduction and many other fields.
If you have an Atomic Force
Microscope (AFM), Electron Microscope, Interferometer, Laser Optical System,
Micro Hardness Tester, or any other special equipment that would be assisted by
our vibration isolation, simply complete the giveaway submission form and send
it back to
edgiveaway@minusk.com.
If you're one of the top applicants, we'll send you one of these free vibration
isolators to assist you with your research.
Submission deadline
for applications is February 28, 2025.
*More...
*$25,000 of
retail products will consist of at least one each of the following models of
Negative-Stiffness vibration isolators: WS-4, BM-1, BM-4, BM-8, BM-10 and CM-1.
Based on the information provided within grant forms Minus K may substitute
different models to best accommodate the application and payload
needs. |
|
|
|
|
2023-2024 Winners: Minus K Technology's
Vibration Isolator Educational Giveaway to U.S. Colleges and
Universities
Wabash College - Physics Department
The vibration isolator will be used with their Zeiss 508 Microscope to
conduct experiments utilizing high magnification to image Brownian motion in
time-lapse imaging of chemical precipitation material formation.
Kent University - Physics Department
The vibration isolator will be used for a magnetic tweezer instrument
to be built on it. Fast video imaging (several hundred images per second) is
used to measure the changes in the depth of glass beads (of a few micrometer
diameter).
Texas Christian University
Physics & Astronomy Department The vibration isolator to be used
with their 6-digit RADWAG XA 21.4Y.M microscale to improve precision of small
mass measurements down to 1 microgram.
Indiana University Physics
Department The vibration isolator will be used to for dynamic
micro-optical coherence tomography of the heterogeneous intracellular motion
present in living cells and tissues. |
Check out previous Educational
Giveaway winners: |
|
|
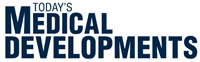 Today's Medical
Developments June 2024 Negative-stiffness vibration isolation, enabling
research into the sub-microns
From the discovery
of exoplanets to the characterization of nanoparticles, much of our most
advanced technological research relies on ultra-sensitive vibration isolation
systems. The best of these is capable of isolating sub-Hertz frequencies and
enables precision research at the sub-atomic level. On the forefront of this
enabling technology is Negative-Stiffness vibration isolation developed by
Minus K Technology
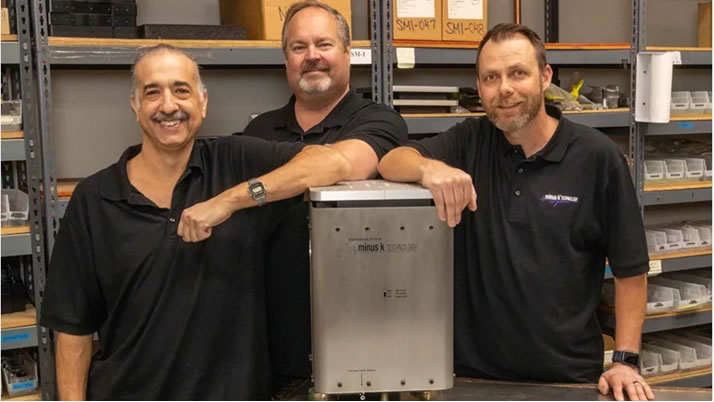 Minus
K Technology principals (L to R) Steve Varma, Erik Runge and Jason Blain,
enable companies, academia and government research laboratories to push the
boundaries of advanced technology.
|
As the need for nano-precision has become
increasingly important in many fields of research and manufacturing such
as microelectronics fabrication, laser/optical system applications, life
sciences, materials, aerospace and biological research so has the need
to implement vibration isolation technology for stabilizing academias and
industrys most critical instrumentation to facilitate operation under
extremely precise requirements operating at atomic-scale
resolutions.
The need to eliminate vibration The need to
provide adequate vibration isolation presents an increasingly important and
complicated challenge, particularly at very low frequencies.
Vibration
influencing high-resolution sub-micron instrumentation can be caused by a
multitude of factors. Within the building itself, the heating and ventilation
system, fans, pumps and elevators are just some of the mechanical devices that
create vibration. How far away sensitive instrumentation is from these
vibration sources, and where in the structure the equipment is located, will
determine how strongly the equipment will be influenced. External to the
building, the equipment can be influenced by vibration from adjacent road
traffic, nearby construction, aircraft, and even wind and other weather
conditions that can cause movement of the structure.
These internal and
external influences cause low-frequency vibration in the 0.5Hz to 50Hz range,
which is transmitted through the structure and into sensitive parts of
instrumentation, compromising resolution, image quality, and the integrity of
data.
Inadequate isolation Many
vibration isolators, particularly at frequencies below 10Hz, deliver limited
isolation vertically and even less isolation horizontally. In fact, such
isolators create vibration isolation problems in the region of their resonant
frequency. All isolators will amplify at their resonant frequency then start
isolating above this frequency. Pneumatic isolators, for example, will amplify
vibration in a typical range of 1Hz to 4Hz. Sensitive instruments, which are
typically manufactured with internal pneumatic isolation, are, therefore, often
subject to problems with vibration.
Another option in use is active feedback
electronic-force cancellation systems, which incorporate the use of sensors,
actuators, and control algorithms to detect and mitigate vibration.
Active systems have limited dynamic range,
however. They have a tough time dealing with vibration input that is either too
large or too small. Vibrations that are too large can cause the system to go
into positive feedback. Vibrations that are too small may not even be detected.
To achieve a high level of precision in vibration-critical applications,
feedback electronic-force cancellation systems must balance a complexity of
inertial feedback in response to incoming vibrations. This can be challenging
for active systems when the inertial feedback is applied to incoming
low-frequency vibrations horizontally.
As sub-micron research continues to advance
at an accelerated rate, the need to protect sensitive instrumentation
like electron microscopes, scanning tunneling microscopes, laser
interferometers, and optical profilers with better vibration isolation
is critical.
Negative-stiffness the technology
behind sub-micron advanced technology There is a more advanced
vibration isolation technology in use when it comes to protecting sensitive
sub-micron instrumentation to low-Hertz vibrations. Introduced in the mid-1990s
by
Minus K Technology, Negative-Stiffness vibration
isolation has been widely accepted for vibration-critical
applications, largely because of its ability to effectively isolate lower
frequencies, both vertically and horizontally.
Full
article...
|
|
Previous
Newsletters
|
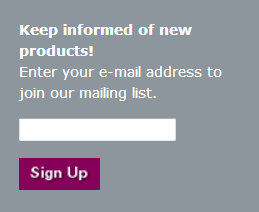
 |
|
|